Notepad++: Absolutely Free G-Code Editor With Code Highlighting
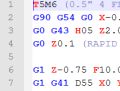
Quite often I see people asking which text editors others use to work with their G-Code.
Some even suggest paid ones.
I am using a free general-purpose advanced text editor called Notepad++.
It is so flexible, it can recognize the language you are working with and turn on the language-specific highlighting for even the G-Code.
I created my own Language profile for it. It is attached to this article so that everyone can download it.
Below is how you can apply this language profile to turn on g-code highlighting: