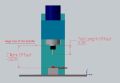
Did you know there are three ways you can touch off your tools?
Because of how Machine Offsets add up, there are several ways CNC machinists can set their Tool and Work Offsets.
This is especially true for Tool Length Offsets.
Tool Offsets can be either Positive or Negative.
Depending on your Machine Shop equipment you should use one or the other.
Regardless of how you set your tool length offset, you apply it the same way.
Right after the tool change and after turning on your spindle and moving to your X Y position above the part.
The very first absolute Z movement should be the line where you apply the tool length offset.
Code
T15 M6; (TOOL CHANGE)
G0 G54 G90 X1.0 Y1.5 S1500 M3;(APPLY WORK OFFSET, MOVE TO THE FIRST POSITION, TURN ON THE SPINDLE)
G43 Z2.0 H15; (APPLY TOOL LENGTH OFFSET WHILE MOVING TO 2.0" ABOVE THE PART)
G0 Z0.1 M08;(MOVE TO FEED HEIGHT AND CARRY ON WITH THE PROGRAM..)
Positive Tool Offsets (gage line tool length offsets)
In the case of Positive Tool Offsets, the offset represents the Length of the tool measured as a distance from the Gauge Line of the spindle (typically spindle nose) to the tip of the tool. The longer the tool, the larger your Tool Length offset will be.
Read More