Rev Up Your Tools - Boost the Productivity!
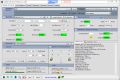
As unhappy I am to learn that something may be wrong with the software I develop and love, negative feedback is essential in learning whether i am doing everything right.
So a couple of days ago I received an email from a somewhat disappointed user.
He (lets call him Peter) was complaining that HSMAdvisor calculator gave him "excessively high" speeds and feeds for his 3/4" 4 flute 3.0 LOC end mill in aluminum.
With the data Peter entered he was getting around 10000 RPM(SFPM 2117) and the feed of 270 inches per minute while usual practice in the shop was side-milling aluminum at that (2.8" axial) depth at only 325 SFM
After double-checking the numbers I replied that in fact his numbers seemed very slow and if for some reason he HAD to run that slow (heck, i machine most steels faster than 325 SFM) due to some conditions, perhaps, he was ought to change the conditions themselves.
This is what I am getting for Peter's end mill setup: