HSMAdvisor 1.304 Released!
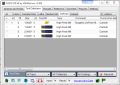
This update fixes the no-message shutdown when your trial expires!
What else is new and improved in this update:
- Fixed no-message shutdown upon expiration of the trial.
- Improved cutting speeds and feeds for milling.
- Added 416 SS material
- Added "Insert" check box and input field to treat Tools as if they were inserts.
- Added internal "Copy/Paste" functionality to quickly populate custom S&F tables.
- Added icons to the bottom taskbar.
- Installer now checks which .NET version you are running and offers to download if it is missing.
Below are most of the new features in a nutshell:
Happy Canada Day!
I would like to congratulate all Canadians and all our Canadain users in particular today.
Wishing peace and prosperity to us all.
Have a nice and safe long weekend!
HSMAdvisor 1.303 Released
Latest update has some important features and improvements.
New and improved in this update:
- New T-Slot cutting tool type. Also known as Woodruff cutter.
- Fixed Startup issue
- Improved DOC/WOC suggestion.
- Reduced executable size.
New T-Slotting tool type
HSMAdvisor inheritantly supported calculating cutting parameters for T-Slotting (Woodruff) cutters before. All that needed to be done was to specify prope shank size and helix angle.
Programming Lesson: 304 Stainless on Low-Power Mill
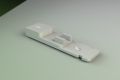
One of HSMAdvisor users asked me for help figuring speeds and feeds for machining stainless on his underpowered Tormach 700.
He volunteered to send me a model to work on, so I decided it was a good opportunity to make a learning video and share it with everybody.
I must say programming for such a low-power machine is a lot harder than for a full-blown production VMC where you are not worried about stalling your machine with anything under 1" in diameter:
Your thoughts and comments are always welcome.
We are actually listening to our users!
FSWizard v1.49 Released (Now for IPhone Too)
I have been working hard to improve not only HSMAdvisor lately, but FSWizard Mobile CNC Machinist App too!
The latest update improves productivity, speed, fixes a lot of small glitches.
And it also adds a completely new GD&T reference tab to both the FSWizard Free and PRO apps.
Update: FSWizard PRO and Free apps have just been approved by the iTunes and are available on the AppStore!
HSMAdvisor 1.301 Released!
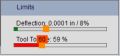
There had not been any updates to HSMAdvisor for several months now.
And there is a very good reason for that.
We have been working hard on a lot of new super-cool features and improving the old functionality.
BTW: This Update Resets the Trial Counter!
Let us cut to the chase.
Here is a list of all the latest changes and improvements:
- New Cut Cloud controls added (beta only!)
- New Cast Aluminum materials
- New combined Tool Torque and Deflection Limit controls
- New and Improved Tool Display Graphics. Now for Turning too!
- Lathe Tools now consider Shank size when suggesting chip-load.
- New Mass Edit - > Set SFM/Feed Overrides command in the Tool Database
- Improved Tool Deflection calculations
- Improved and refined a lot of behind-the-scenes stuff
I am going to explain the most important improvements below.
We are Going Social
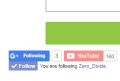
As you may have noticed zero-divide.net website where I post all the updates, research and news have gotten a bunch on new social sharing buttons.
I would like to encourage all our friends to share our web pages with the big wide net!
As I am beginning to realize the potential behind the whole "social networking" thing, I also understand that this is something I should have done from the get-go.
Help this project flourish by recommending our great software and information to your peers on the Facebook, Google+ and LinkedIn!
Best High Speed Machining is Dry Machining

Have you ever wondered how much tool life can deteriorate when using coolant with High-Speed Machining (HSM)?
Or maybe you never really saw the boost in tool life when using HSM techniques because you had to use coolant?
Well, here is a test result I just got from running the same tool at the same Speed and Feed with and without coolant.
6 ways to utilize your CNC spindle (and make your life easier)
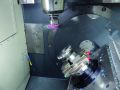
We all know what the CNC Milling Machine spindle is used for - to hold the tool. But it is old and boring. Everybody does that.
Here are the 6 interesting and maybe less common ways to utilize machine spindle, increase productivity and solve some problems you never thought you had.
Use your Spindle as a fan to blow chips and coolant off of your work-piece, table and fixturing.
I saw this little gadget at a local IMTS show and it was quite cool. It is installed into a tool holder like a regular cutting tool would be and at the end of the program you can call the it up and run a little table-cleaning program to make your work a lot cleaner!
Combating Chatter: 4 reasons to NOT reduce your feedrate
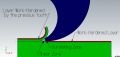
We all have heard hundreds of times that when chatter is happening during machining, we should reduce our feed rate. The same advice we also hear for compensating for extra-long tools and unstable setups.
Let me explain why I think this is mostly incorrect.
Let’s list the effects of reducing the feed rate:
- Reduces tool life.
- Reduces productivity.
- Increases deflection.
- Causes chatter.
Let me explain from my own experience and research I have made each of these points and a simple way to avoid chatter's adverse effects.Read More