HSMAdvisor 1.304 Released!
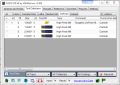
This update fixes the no-message shutdown when your trial expires!
What else is new and improved in this update:
- Fixed no-message shutdown upon expiration of the trial.
- Improved cutting speeds and feeds for milling.
- Added 416 SS material
- Added "Insert" check box and input field to treat Tools as if they were inserts.
- Added internal "Copy/Paste" functionality to quickly populate custom S&F tables.
- Added icons to the bottom taskbar.
- Installer now checks which .NET version you are running and offers to download if it is missing.
Below are most of the new features in a nutshell:
HSMAdvisor 1.301 Released!
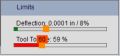
There had not been any updates to HSMAdvisor for several months now.
And there is a very good reason for that.
We have been working hard on a lot of new super-cool features and improving the old functionality.
BTW: This Update Resets the Trial Counter!
Let us cut to the chase.
Here is a list of all the latest changes and improvements:
- New Cut Cloud controls added (beta only!)
- New Cast Aluminum materials
- New combined Tool Torque and Deflection Limit controls
- New and Improved Tool Display Graphics. Now for Turning too!
- Lathe Tools now consider Shank size when suggesting chip-load.
- New Mass Edit - > Set SFM/Feed Overrides command in the Tool Database
- Improved Tool Deflection calculations
- Improved and refined a lot of behind-the-scenes stuff
I am going to explain the most important improvements below.
Combating Chatter: 4 reasons to NOT reduce your feedrate
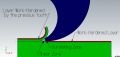
We all have heard hundreds of times that when chatter is happening during machining, we should reduce our feed rate. The same advice we also hear for compensating for extra-long tools and unstable setups.
Let me explain why I think this is mostly incorrect.
Let’s list the effects of reducing the feed rate:
- Reduces tool life.
- Reduces productivity.
- Increases deflection.
- Causes chatter.
Let me explain from my own experience and research I have made each of these points and a simple way to avoid chatter's adverse effects.Read More
One Case of HSM Machining: HSMAdvisor vs. All
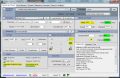
Look for the HSM machining of the round central pocket in the beginning.
Here we have a 12mm 6 flute Coated hi-performance endmill, cutting 1" deep at 0.047" (10%) rWOC.
at 10000 RPM and 300 ipm feedrate. the chipload works out to be 0.005". Material is 4140 pre-hardened steel.
Impressive isn't it?
Those results have been achieved with uber-expensive BlueSwarf tap-test technology.
This is one video that caught the eye of one of my HSMAdvisor trial users:
Being a geek and wanting to help the user make the right decision I immediately punched the numbers into my HSMAdvisor app.
Here is what I've got:Read More
The New Help Category: Tool Database & Inventory
Being as vast and as complex as it is HSMAdvisor Tool Database may seem overwhelming for many users despite all the benefits of using it.
To address this issue I have just added a new category to our HSMAdvisor on-line Help resource called Tool Database & Tool Inventory
Here is a the opening article of that category:
An integral part of HSMAdvisor is its very powerful Tool and Cut Database also known as Tool Database
Tool Database allows you to not only store your tools in one convenient location sparing you the time needed to key-in your tool type, size etc.
It is very extensible and since its inception has grown both in size and functionality.
With every update the list of its features keeps growing and at present it can (among many other things) do the following:
- Store and Edit geometric Tool data, Including automatic creation of tool data from a sample tool entry.
- Store/Create/Manage Custom Tool Manufacturer Cutting data using Manufacturer Brand/Series names
- Store and Manage Tool Handling data like: Number of Tools in stock, Ordering Vendor Information, Physical location in the shop
- Set up Low Tool Stock warning levels and add tools, that are low on stock to a Request List to be ordered.
- Create and Export customizable Tool Request Orders for use in purchasing.
- Restock received tools into the Tool Database
- Attach Cutting Data (Known as just "Cuts") to tools for various cutting scenarios in different materials.
- Store complete MasterCAM Tool and ToolPath parameters for easy importing/Exporting of MC operations
- Organize Tools into Libraries
- Share a single Tool Database between many HSMAdvisor seats in real-time.
In the following articles we will describe the main functions of the Tool Database
In all there are 5 articles in there already describing many of its functions in detail.
Please check them out if you are not sure what the Tool Database does and how to use it.
And as always: when in doubt - ASK :)
HSMAdvisor v1.217
We have just released a pretty important HSMAdvisor v1.217 update!
I strongly encourage everybody to go ahead and install it as it contains some big improvements.
What is new and improved in this update:
- New Tool Database Status Indicator:
Status Bar Indicator showing whether the Database file is being written, up to date or if write has failed - A Warning now shows up when HSMAdvisor is closed with DB changes not saved.
- Now you can not close HSMAdvisor until Database file has been written to the disk
- A local backup copy of Shared database is now created on each computer for cases when connection is unavailable.
- Fixed the problem when new Tools and Cuts were not added to the shared database
- Fixed some (./,) locale-related problems.
- Fixed the problem of some settings not being saved.
I would like to explain one new feature here - The Tool Data Base Status indicator:
On the status bar of HSMAdvisor screen you can now see The Tool Data Base Status indicator (later DB Status) icon.
Tool Inventory Advisor: Workflow Overview
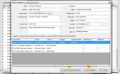
TiAdvisor (Tool Inventory Advisor) is a new feature under development within HSMAdvisor.
Unlike most cases when developers design a standalone product and then go through a laborious work of integrating it into existing software products, i decided to go the other way.
TiAdvisor will be developed as an integral part of HSMAdvisor and then, once complete, will be moved into a separate standalone product. This will make for seamless integration between our software products.
What TiAdvisor does
- Keeps track of inventory levels.
- Automatically add tools that are low in stock to Purchase Request List
- Generate and print Purchase Request form
- Add tools to stock when they are received
More functions are being worked on.
Download TiAdvisor bundled with HSMAdvisor over here: http://zero-divide.net/index.php?page=forums&shell_id=170&article_id=4776
TiAdvisor Workflow
Lesson 5: Everything about CNC Tool Length Offsets. Positive and Negative (G43 g-code, H offset)
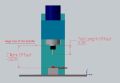
Did you know there are three ways you can touch off your tools?
Because of how Machine Offsets add up, there are several ways CNC machinists can set their Tool and Work Offsets.
This is especially true for Tool Length Offsets.
Tool Offsets can be either Positive or Negative.
Depending on your Machine Shop equipment you should use one or the other.
Regardless of how you set your tool length offset, you apply it the same way.
Right after the tool change and after turning on your spindle and moving to your X Y position above the part.
The very first absolute Z movement should be the line where you apply the tool length offset.
G0 G54 G90 X1.0 Y1.5 S1500 M3;(APPLY WORK OFFSET, MOVE TO THE FIRST POSITION, TURN ON THE SPINDLE)
G43 Z2.0 H15; (APPLY TOOL LENGTH OFFSET WHILE MOVING TO 2.0" ABOVE THE PART)
G0 Z0.1 M08;(MOVE TO FEED HEIGHT AND CARRY ON WITH THE PROGRAM..)
Positive Tool Offsets (gage line tool length offsets)
In the case of Positive Tool Offsets, the offset represents the Length of the tool measured as a distance from the Gauge Line of the spindle (typically spindle nose) to the tip of the tool. The longer the tool, the larger your Tool Length offset will be.
Lesson 4: Essential Stuff about Work Offsets, Tool Length Offsets, G54-G59, Part Zero, G43 H
Before we run any G-Code program, we need to tell the machine where our part zero is.
A Part Zero is simply a bunch of numbers that offset the axis to give the machine a new coordinate point to work from.
Work Offsets is one of the most basic pieces of knowledge any machinist must-have.
Let us account for all the basic coordinate systems and definitions, available in a generic CNC machine
- Machine Home and (Absolute) Machine Coordinates
- Work Offset Coordinates
- Tool Length Offsets
Machine Home and Machine Coordinates: G53
Machine Coordinates (or Absolute Coordinates) is the absolute and constant representation of the machine axis position.
These coordinates never change between Machine Restarts and must remain such. In fact, there is often no way for an operator to adjust the Absolute Machine Axis Home position.
Machine Home is simply that magical place where all Machine Coordinates should become Zero.
To Home the Machine is to start a machine operation, that will move all Axis to their soft limit position where X, Y, and Z-axis reading will be set to zero.
Homing must be done every time you restart your machine. Without it machine does not know where is the position of its table or spindle.
When homed your machine coordinates will read X=0 Y=0 and Z=0 and it is going to look like this:
The point where Machine X and Y intersect is called Table Home Position and the one where the Machine Z-axis starts from is called Spindle Home.
Now, there is no agreement between machine tool manufacturers on where the machine home should be.
New stuff in HSMAdvisor 1.191
We have some (I am sure welcome) addition to our family of tool types supported by HSMAdvisor.
The new tool type is "Boring Head".
This tool is used for finishing holes on milling centres. Also in this release I have made a lot of improvements to operation of myCut Database and revised ssuggested depth of cut for milling tools when used at low radial engagement.
More details on the HSMAdvisor Download page.
Regards!