Finally got my proLIGHT CNC Mill running with UCCNC control software.
Chose that over mach3/4 because uccnc software seemed better made. Unfortunately, it too has bugs.
Most importantly, executing gcode.
Instead of running all codes in a block simultaneously, it does them in the incorrect order.
For example, code like
Code
G55
G0 G90 G54 X0 Y0
Instead of going to X0 Y0 defined in offset #54, it will go to coordinates of offset #55!
Only after executing that line, the offset will change to G55.
Similar issue with
Code
G28 G91 Z0
Don't need to tell you this may lead to crashes.
So I changed the MasterCAM's post processor to output some of the codes in different lines.
Hopefully, devs will fix this issue soon.
In other news, I have just finished the first 2-tool piece.
It was a miniature skull figure made out of aluminum:
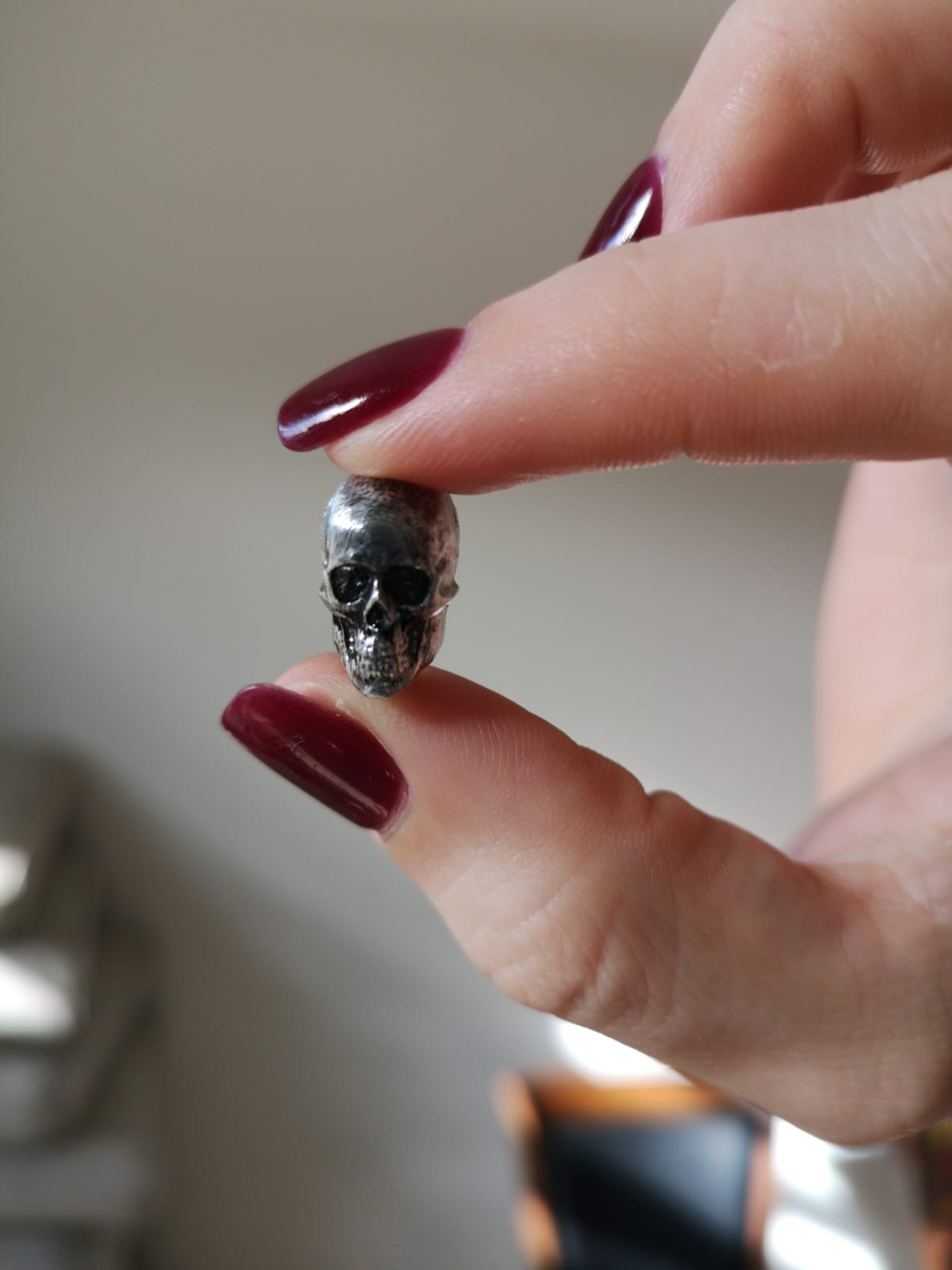
I got 150 bucks for machining that for a guy I met in a Facebook group. Nice!
The smallest endmill was 1mm ball nose, and it held up perfectly at max RPM of 5000 and feed rate of about 25ipm.
The DOC and stepover were about 0.004"
Now I wish it had a 20k spindle. If I could run at 100ipm, it would make a quick work of that little piece.
This way, it took 1 hour, which is not too bad either.
Cheers!