HSM with MasterCam Dynamic Milling has long been one of my favorite toolpath strategies when machining hardened and tough to machine steels.
The job at hand was to machine out a 5" disk out of pre-hardened 4340 steel. About 43RC hard.
Due to an island in the middle (leaving only 3/4" room for the tool) I could not use a bigger indexed cutter, so i decided to use the adaptive clearing toolpath.
I started out by calculating Speeds and Feeds with HSMAdvisor and come up with the following starting parameters:
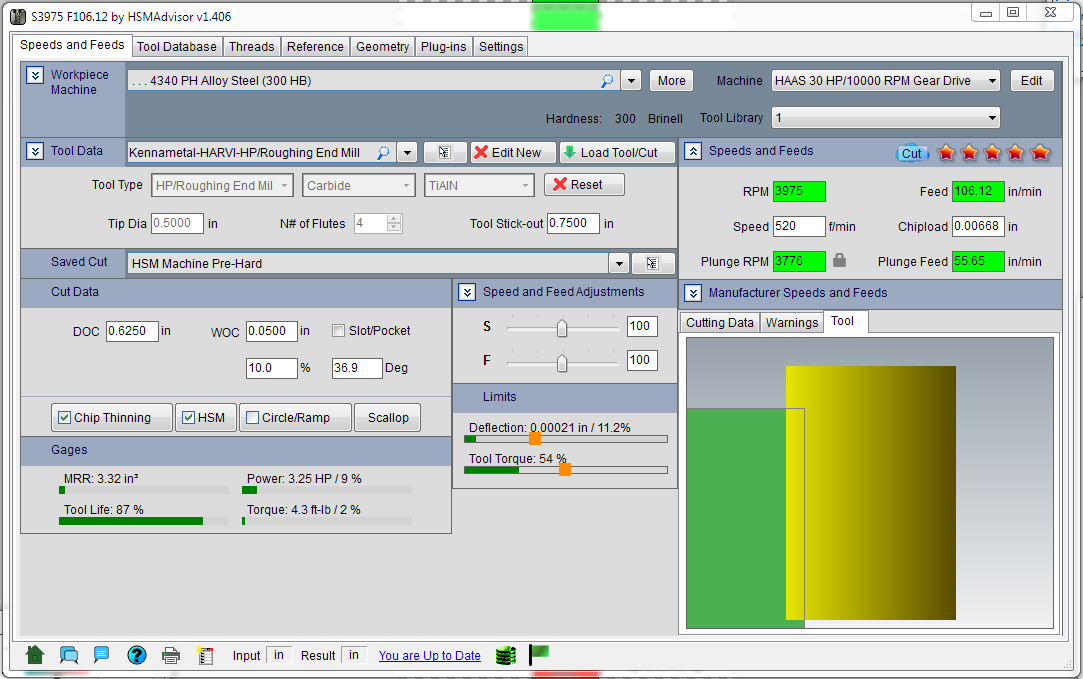
Full depth, at 10% engagement.
Which worked just fine. But the tool was not new and I decided to sacrifice it in the name of science and maxed it up to see how long the tool was going to handle it.
So I adjusted the cutting speed to 170% and feed to 150% (which accounts to heavy roughing):
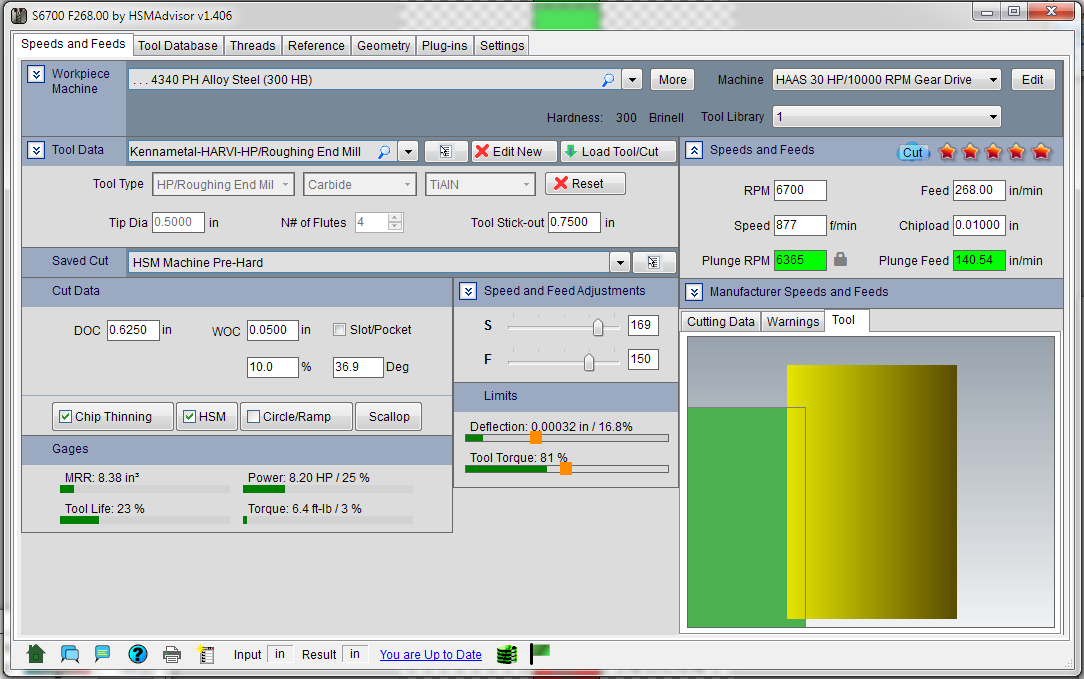
To be honest I was not sure the tool was going to last very long, but it exceeded all my expectations!
It lasted for about 2 hours and completed the whole run of more than 20 pieces.
I even took a video cutting one of the parts:
Note how there are no sparks coming out. This is because the chip is thick enough to not overheat. This works both ways. Chips stay cool and due to their larger mass carry most of the heat away from the cutting edge.
After the end of the run (and it was not new to begin with) the tool looked like it could do as much!