Cautionary tale about Retention Knobs
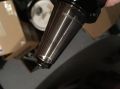
I came across a very educational post on Practical Machinist.
The topic-starter used over-aggressive speeds and feeds for his tiny BT30-taper machine and the retention knob (a.k.a Pull Stud) snapped causing the holder to drop lower, disengage from drive lugs and mess up the spindle bore in the process.
Just in case you don't know. Retention Knob looks like this and is used to pull the tool holder in to the spindle bore, thus holding it in place:
(Retention knob is the detail on the right)
This whole article is to remind everyone the importance of proper tool holder and retention knob maintenance.
Retention Knob Tips
- Retention knobs (according to HAAS) have service life of about 6000-8000 hours.
That means that if a tool holder is used 3 hours a day, you should replace the knob after 8 years in service.
For smaller BT30 knobs, you should probably replace them every 4 years. - Retention knobs should be lightly oiled or greased (if TSC is used) once a month to lubricate the draw bar.
- There should be no visible damage or rust on the knobs.
- Do not exceed the maximum cutting force recommended by your machine manufacturer.
Some of those high-helix end mills create large down-force that could in certain cases cause the knob to snap! - Also retention knobs should be torqued to manufacturer specs and the tightness should be regularly checked. Overtightened knobs may lead to taper of the tool deforming and causing uneven contact with the spindle bore.
Tool Holder Maintenance Tips
- Keep Tool Holders clean. Especially the taper part that is matching to the spindle bore.
Wipe them with a clean cloth. - Do not use sand paper to clean tool holders! Soft Scotch-brite is acceptable to clean very dirty ones.
- Repair dings and notches on the taper.
Even an aluminum chip will cause a ding, that will create a high spot around it. - Replace worn-out tool holders with new ones.
Signs of ageing is uneven contact with the spindle bore and fretting (blackening of taper in certain spots) - It is also a good idea to re-grind the spindle as well when replacing the tool holders - there are lot's of services that do that for very reasonable price.
- Like wise when a new machine is purchased, only new holders and retention knobs should be used. Using old worn out holders on a new spindle bore will lead to its premature wear and even damage.
Those are all the things I could think of at the moment.
Let me know if there is anything missing.
Have a safe and productive week!