Calculating cutting parameters for custom or form tooling inside HSMAdvisor
September 10, 2013, 5:00 pmArticle Summary
Eldar Gerfanov (Admin)
September 10, 2013, 5:00 pm
Eldar Gerfanov (Admin)
September 25, 2013, 8:24 pm
41667
Public
Author Summary
Tue September 2, 2025, 3:03 pm
Tue September 2, 2025, 3:03 pm
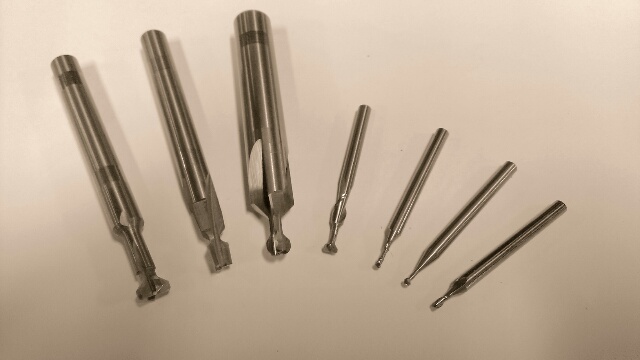
If you are working in mold-making, prototyping or even in a job shop you have had to use unusual form tooling before in your life.
Form tooling is often used to machine undercuts and other features on regular 3 axis machines that would otherwise require a multi axis machining centre or are not machinable o at all.
The classical example of a form tool is a tear-drop ball mil, also known as a "lollipop". It has a tip with a certain diameter and a much smaller shank that produces enough clearance to machine undercuts on straight walls. It can also be used to regular surface finishing and 2d milling.
Another example is a T-slot cutter that is used to produce key-ways and t- slots
The main thing to consider when machining with reduced shank end mils is deflection and torque.
While deflection is especially dangerous for long tools, torque becomes much more important for tools with severely reduced shank.
Torque required to break a tool is directly proportional to the diameter of its shank.
And when shank diameter is much smaller than the tip diameter it does not matter how short that weak portion is: unless you compensate for it you will snap the tool.
The first thing that crosses the mind in many such cases is "I gotta run this tool very slow". It may take forever, but in many cases job gets somewhat done.
Contrary to that many experienced machinists have been proponents of different approach. Instead of reducing feed rate to the point of rubbing and below, it is much more productive to reduce cutter engagement if possible and leave feed rate settings largely unchanged.
Trying to keep proper chip load is even more important when machining work-hardenable materials like stainless steel and titanium. In those cases rubbing is not just unproductive, it leads to a very premature, in many cases instantaneous tool failure.
Just how much of a cut is possible to take in each particular case is the black magic that separates beginners from seasoned pros.
Not to worry though
Here is an example on how to setup a form tool on HSMadvisor.
First, this is how our setup looks:
We start up the calculator and simply enter as much known information as possible.
There is a little trick.
Because the distance from the tip to the end of necked portion is shorter than the total stick out, we should assume that distance as Effective Stickout and use it for our calculations
Your calculator window should look like this:
Notice the torque warning.
What it tells you is that calculator had to limit the feedrate in order to keep the tool from snapping.
This is not an ideal situation as chipload is very small and this will lead to rubbing.
It also tells you what to do.
Simply move the Tool Performance slider to the left until we get a better chipload and/or the warning disappears:
Notice now the chipload is much better and even though calculator still limits the feedrate in order to keep within the allowed torque spec, we can live with that.
There is simply no way to make the cut we want without some sort of feedrate compensation.
If we wanted to get the optimal chipload we would have to further reduce width or depth of cut manually.
I actually used this exact tool and speed and feed recommended by HSMAdvisor to machine a real-world aluminum mold.
I just trust my calculator so much.
This tool has been used many times by us before and every time we tried to take the full 0.070" width of cut at 6000RPM and 5 ipm. Anything harder would just snap the cutter.
Still we had bad surface finish and alot of chatter.
Simply by using smaller width of cut we were able to go faster, improve the tool life and the surface finish.
JK
Thanks for the tutorial! I have long wondered if your calculator could accurately predict S&F for such cutters. I am going to give it a whirl. One question, how does it know whether I am using coolant or not?
Eldar Gerfanov (Admin)
Austin Floyd
Great tutorial, could definitely come in handy should that need arise!!