Before we run any G-Code program, we need to tell the machine where our part zero is.
A Part Zero is simply a bunch of numbers that offset the axis to give the machine a new coordinate point to work from.
Work Offsets is one of the most basic pieces of knowledge any machinist must-have.
Let us account for all the basic coordinate systems and definitions, available in a generic CNC machine
- Machine Home and (Absolute) Machine Coordinates
- Work Offset Coordinates
- Tool Length Offsets
Machine Home and Machine Coordinates: G53
Machine Coordinates (or Absolute Coordinates) is the absolute and constant representation of the machine axis position.
These coordinates never change between Machine Restarts and must remain such. In fact, there is often no way for an operator to adjust the Absolute Machine Axis Home position.
Machine Home is simply that magical place where all Machine Coordinates should become Zero.
To Home the Machine is to start a machine operation, that will move all Axis to their soft limit position where X, Y, and Z-axis reading will be set to zero.
Homing must be done every time you restart your machine. Without it machine does not know where is the position of its table or spindle.
When homed your machine coordinates will read X=0 Y=0 and Z=0 and it is going to look like this:
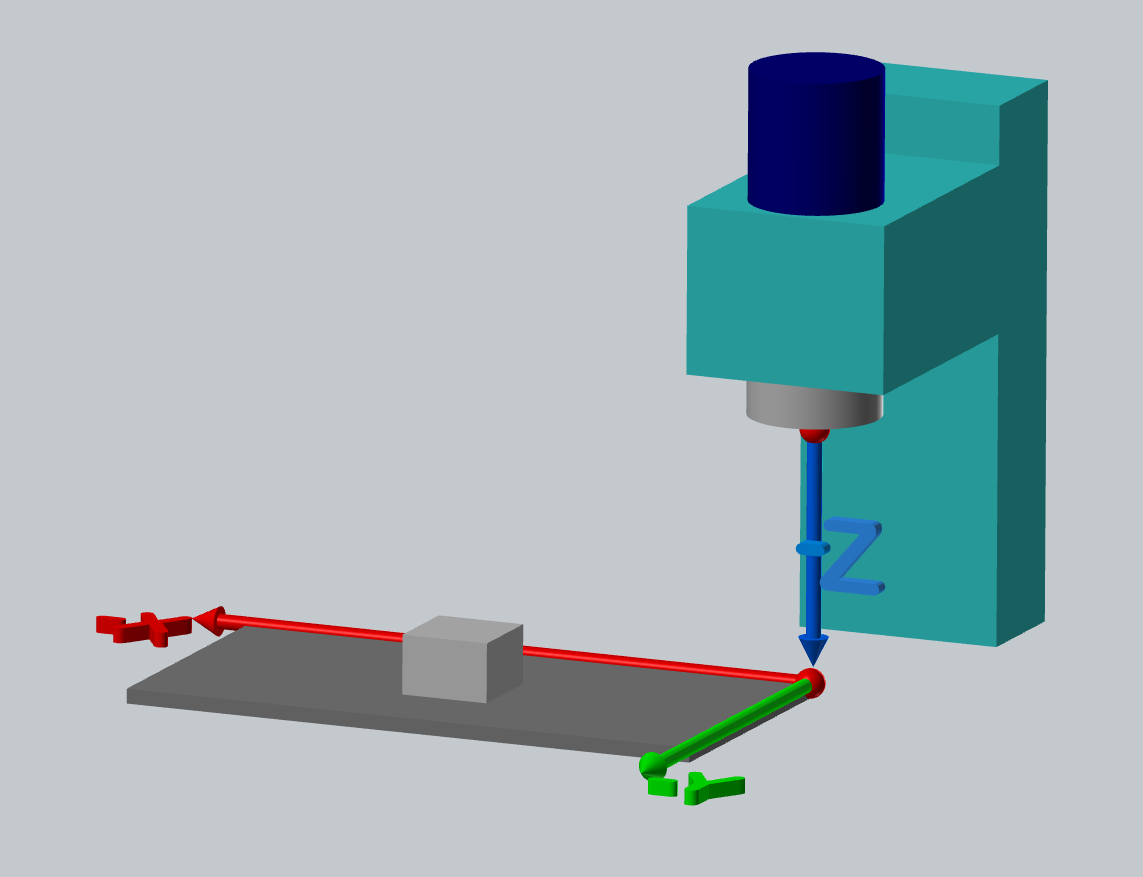
The point where Machine X and Y intersect is called Table Home Position and the one where the Machine Z-axis starts from is called Spindle Home.
Now, there is no agreement between machine tool manufacturers on where the machine home should be.
Read More